Online-Konfigurator für das schnelle und individuelle Design von Induktoren und Zahnrädern
Mass Customization in der Industrie mithilfe des Konfigurators von morgen
Die bedarfsspezifische Erstellung von industriellen Komponenten wie Induktoren und Zahnrädern bietet Kunden funktionale Mehrwerte und für Anbieter innovative Differenzierungsmöglichkeiten. In Kooperation mit dem Berliner Softwareunternehmen trinckle entwickelte PROTIQ für Ihren Marketplace webbasierte Konfiguratoren, mit dem Kunden in wenigen Minuten kundenspezifische Kupferinduktoren und Zahnräder aus Kunststoff oder Metall adaptieren und direkt bestellen können.
Die innovativen Konfiguratoren auf dem PROTIQ Marketplace überzeugen durch ihre intuitive Bedienbarkeit und einen kosteneffizienten Design-Prozess
Im Zeitalter von Industry 4.0 sind immer kürzere Produktlebenszyklen, höhere Spezialisierungsgrade und höhere Individualität gefragt. Die digitale Fabrik der Zukunft muss daher sehr flexibel in der Kleinserien- und sogar Einzelstückfertigung sein. Beispiele für Industrieprodukte, bei denen oftmals sehr bedarfsspezifische Anforderungen an die Geometrie vorliegen, gleichzeitig aber nur geringe Stückzahlen benötigt werden, sind Kupferinduktoren und Zahnräder.
Industrielle Kupfer Induktoren - ein idealer Anwendungsfall für additive Fertigung
Induktive Erwärmung ist ein beliebtes Heizverfahren in der metallverarbeitenden Industrie, denn es erweist sich als prozesssicher, energieeffizient und präzise steuerbar. Zu diesem Zweck wird eine Induktionsspule mit einem Wechselstrom beaufschlagt, sodass sich ein Magnetfeld bildet. Bringt der Anwender nun ein leitfähiges Bauteil in das Magnetfeld ein, wird ein elektrischer Strom erzeugt und das Bauteil erhitzt sich auf eine definierte Zieltemperatur. Grundvoraussetzung für eine schnelle und homogene Erwärmung ist die Form des verwendeten Induktors. Je besser die Induktionsspule an das Werkstück angepasst wird, desto effizienter und homogener ist die Erwärmung.
Daher müssen Induktionsspulen für verschiedene Anwendungsbereiche eigens konstruiert und produziert werden. Vom Auftrag bis zur Fertigstellung eines Induktors können bei konventioneller Fertigung durch händisches Biegen oder Löten jedoch Wochen oder sogar Monate vergehen. Die additive Fertigung bietet hier in mehrfacher Hinsicht eine aussichtsreiche Alternative. Da die digitale Fertigungstechnologie ohne Werkzeuge und Formen auskommt, lassen sich spezifische Geometrien für jeden Anwendungsfall herstellen, ohne dass sich die Produktionskosten dadurch erhöhen. Darüber hinaus eignet sich die additive Fertigung besonders für die Herstellung komplexer Geometrien. Im Falle der Induktoren bedeutet dies, dass sich die Geometrien mit ihren Spulenwindungen und inneren Kanälen sehr viel präziser auf das jeweilige Werkstück anpassen lassen, als es durch konventionelles Biegen oder Löten möglich gewesen wäre. Ebenfalls zeichnen sich additiv gefertigte Induktoren dadurch aus, dass sie durch den Wegfall des konventionellen Lötprozesses mehrerer Komponenten keine Sollbruchstellen in der Geometrie aufweisen, sodass sie mit einer höheren Standzeit überzeugen können. Grundvoraussetzung für die Herstellung von Induktoren mittels additiver Fertigung ist die Verarbeitung von hochleitfähigen Materialien. Kupfer lässt sich allerdings mit der aktuell Verfügbaren Anlagentechnik nicht verarbeiten, da die genutzte Laserstrahlung nahezu komplett reflektiert wird. Die PROTIQ GmbH hat seit 2013 einen einzigartigen Prozess, der die Verarbeitung von hochleitfähigem Kupfer ermöglicht.
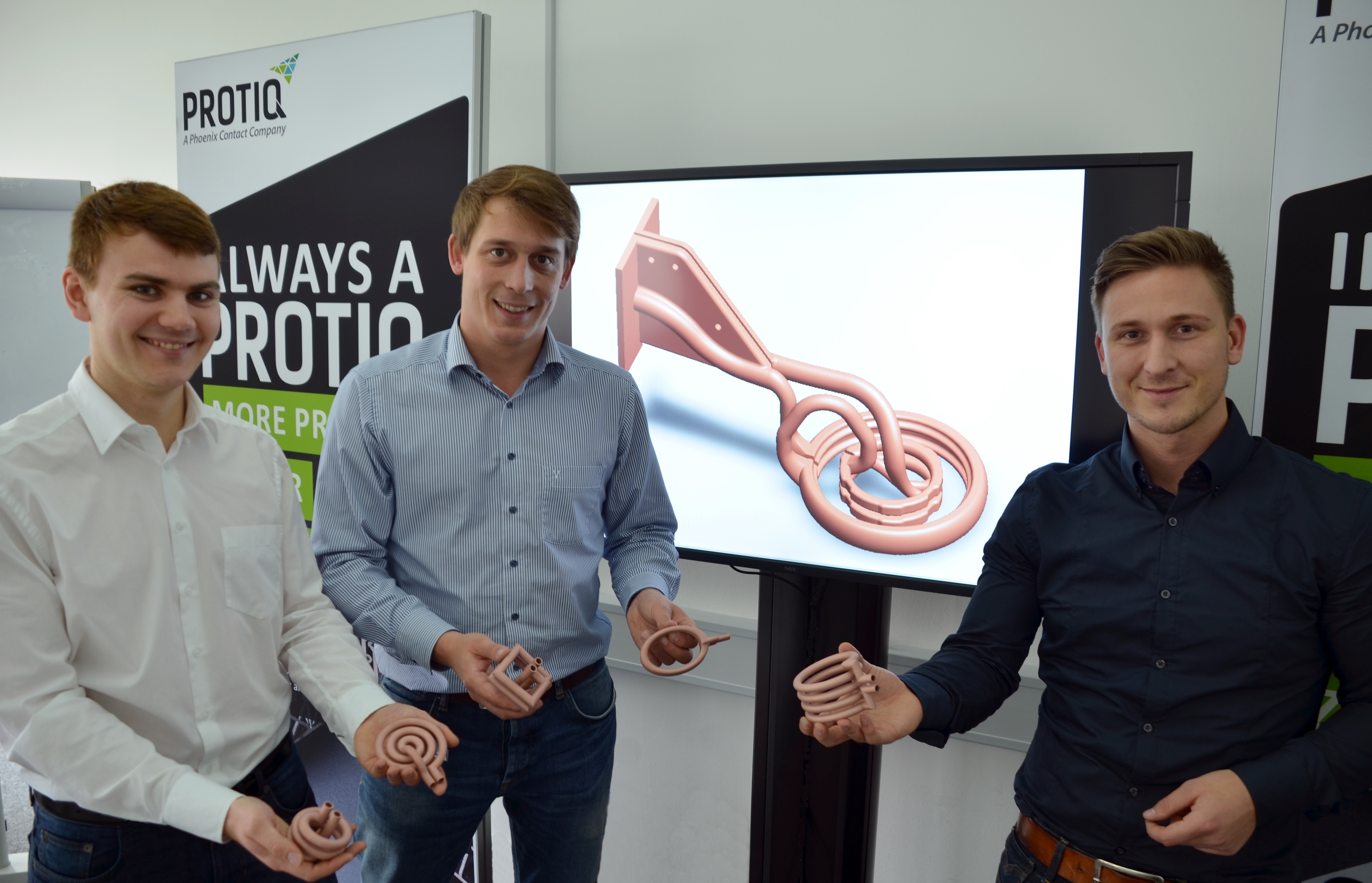
Bedarfsgerecht konfigurierbare Zahnräder – die perfekte Übersetzung für zahlreiche Einsatzbereiche
Eine vielversprechende Applikation für die additive Fertigung bildet ebenfalls der Bereich der Zahnräder. Additiv gefertigte Sonder-Zahnräder für geringe Stückzahlen adressieren die hohe Geschwindigkeit sowie die Entkopplung der Stückkosten von den Stückzahlen in der additiven Fertigung. Sondergeometrien können ohne die Erstellung von kostenintensiven Werkzeugen wirtschaftlich und schnell produziert werden. Einen besonderen Anforderungsbereich stellt weiterhin das Ersatzteilmanagement dar, bei dem keine CAD-Daten vorliegen. Im Oldtimersegment tritt oftmals der Fall auf, dass aufgrund von abgenutzten oder beschädigten Geometrien, ein Reverse-Engineering Prozess an seine Grenzen stößt, da das gewünschte Design nicht vollständig reproduziert werden kann. In diesem Fall besteht die Möglichkeit eine Nachkonstruktion auf Basis einer technischen Zeichnung zu erstellen, jedoch bedingt dieser Prozess einen enormen Zeitaufwand sowie tiefergehende CAD-Kenntnisse.

Der manuelle Designprozess als Engpass
Eine entscheidende Hürde gilt es zu überwinden, bevor individuelle Bauteile bedarfsgerecht gedruckt werden können: den Entwurfsprozess der einzelnen Geometrien. Die Generierung dieser Konstruktionsvarianten in einem konventionellen CAD-Konstruktionsprozess ist mit vielen manuellen und wiederkehrenden Konstruktionsaufgaben verbunden. Dieser zeit- und kostenintensive Design-Workflow ist der Engpass für das Angebot vieler kundenindividueller Anwendungsfälle der additiven Fertigung.
Mit neuartigen CAD-Softwarelösungen lassen sich derartige regelbasierte Designaufgaben automatisieren.
Auf dem PROTIQ Marketplace können Kunden sowohl Induktoren als auch Zahnräder in wenigen Minuten passgenau konfigurieren. Innerhalb der Online-Konfiguratoren, die auf der trinckle Software „paramate“ basieren, wählen Nutzer dazu einfach die benötigte Basisgeometrie für ihre Anwendung und bestimmen einzelne Parameter. Algorithmen kontrollieren dabei die Interdependenzen von mehr als zwanzig verschiedenen Parametern, sodass die Baubarkeit und Funktionalität jedes Modells sichergestellt ist. Weiterhin wird bei jeder Anpassung eine unmittelbare Aktualisierung des Live-Preises durchgeführt, sodass eine sofortige Beauftragung möglich ist. So kann der Kunde auch bei der Nutzung der innovativen Konfiguratoren die volle Flexibilität und Schnelligkeit des PROTIQ Marketplace genießen.
Kernidee: Design-Automatisierung
Statt zahllose, hochkomplexe Konstruktionsschritte manuell zu durchlaufen, dauert der Konfigurationsprozess im Web-Konfigurator nur wenige Minuten und es entsteht ein für die additive Fertigung optimiertes Design, für das auch erfahrene CAD-Konstrukteure einige Stunden investieren müssten. Trotz der sehr komplexen Geometrien und zahlreichen Adaptionsmöglichkeiten ist die Bedienung der Konfigurationsoberfläche intuitiv und einfach.
Was bedeutet dies im Detail? - Der Endkunde profitiert von dieser Zeit- und Kostenersparnis. Im Vergleich zum manuellen Konstruktionsprozess in herkömmlichen CAD-Systemen, der mehrere Stunden dauern kann, dauert der Konfigurationsprozess weniger als 5 Minuten. Das bedeutet für den Nutzer eine enorme Kostenreduktion bei jedem Bauteil. Konstruktions-Knowhow ist nicht erforderlich. Der zeitraubende Kommunikationsprozess zwischen Kunden und Konstrukteur zur Abstimmung der Designanforderungen sowie Austausch von Konstruktionsdaten entfällt. Dank der additiven Fertigung und der Automatisierung des Konstruktionsprozesses gehören Lieferzeiten von mehreren Wochen oder sogar Monaten der Vergangenheit an, sodass die Kunden das fertige Modell bereits nach wenigen Tagen in ihren Händen halten können.

Auftakt zu einer intensiven Partnerschaft: PROTIQ & trinckle
Für PROTIQ und trinckle bilden diese beiden Projekte die Basis einer engen Zusammenarbeit. Durch die hohe Flexibilität und Schnelligkeit sowie dem besonderen Ziel, am disruptiven Markt der additiven Fertigung innovativ zu agieren, können sich die beiden jungen Unternehmen optimal unterstützen und daraus resultierende Synergieeffekte zielführend nutzen.
Weitere News
Ihre 3D-Dateien sind bereits fertig?
Laden Sie einfach Ihre Daten hoch. Alle Dateien werden automatisch geprüft und für den Druck optimiert.