Gesteigerte Produktivität durch Automatisierung entlang der Prozesskette in der Additiven Fertigung
Die Additive Fertigung bietet ein enormes Potenzial für industrielle Anwendungen durch eine signifikante Steigerung der konstruktiven Gestaltungsfreiheit im Vergleich zu konventionellen Fertigungsverfahren. Um die Vorteile dieser neuen Freiheitsgrade besonders unter dem Aspekt der Wirtschaftlichkeit sinnvoll umsetzen zu können bedarf es der Automatisierung und Verkettung von manuellen Prozessschritten im 3D-Druck. So lässt sich die Produktivität in großem Maße steigern und die Additive Fertigung auf eine neue, industrielle Ebene bringen. Auch bei Protiq spielt die Automatisierung seit dem Livegang der online Plattform im Dezember 2016 eine bedeutende Rolle und bildet das Fundament des digitalen Geschäftsmodells.
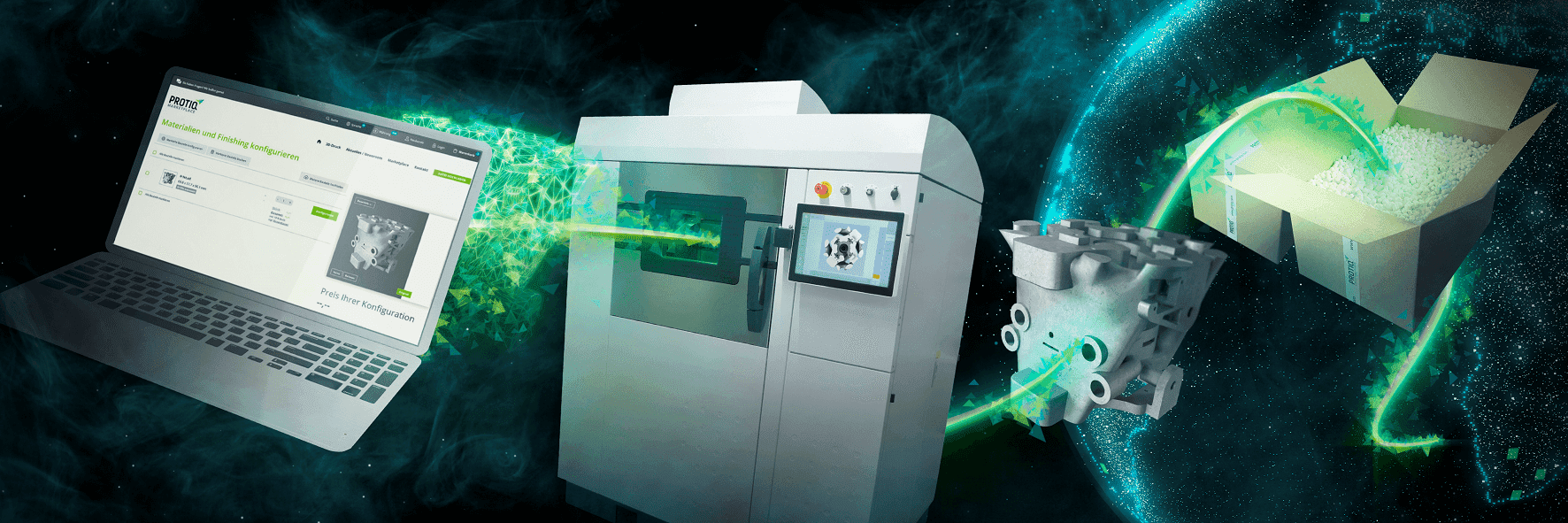
(Prozess Webseite) Vollständige und intelligente Verkettung sowohl auf digitaler als auch analoger Ebene: Bei Protiq startet die Automatisierung bereits auf der digitalen Plattform und begleitet entlang der gesamten Prozesskette.
Die Automatisierung wurde bereits vor der Ausgründung von der Muttergesellschaft vorgelebt
Bereits vor der Ausgründung als Tochtergesellschaft der Phoenix Contact GmbH & Co. KG konnte die ehemals unter dem Namen „Rapid Solutions“ bekannte Einheit des Werkzeugbaus die Vollautomatisierung und die damit einhergehenden Herausforderungen im Bereich der konventionellen Fertigung hautnah mitverfolgen. Der interne Werkzeugbau von Phoenix Contact zählt zur Spitze in seinem Bereich und den besten im deutschsprachigen Raum. Als Teilnehmer des angesehenen Wettbewerbs „Excellence in Production“, wurde der Werkzeugbau bereits zweimal zum Gesamtsieger und „Werkzeugbau des Jahres“ gekürt. Nicht zuletzt konnten diese Auszeichnungen durch eine konsequente Umsetzung der Industrie 4.0 erreicht werden. Das zeigt sich besonders in einer voll verketteten, automatisierten Produktionszelle. Dieser Spirit in Bezug auf den technologischen Fortschritt sowie dem kontinuierlichen Drang nach Innovation sollte auch bei der ausgegründeten Tochtergesellschaft von Beginn an Teil der Unternehmens-DNA werden. Dementsprechend wurden Lösungen zur Automatisierung von manuellen Prozessschritten bereits bei der Entstehung der Protiq berücksichtigt. Hierbei sind sowohl die digitale Seite auf Basis der kontinuierlich wachsenden Plattform als auch die analoge Seite in Form einer intelligenten Verkettung in der Produktion essentielle Faktoren gleichen Gewichts. Diese fließen auf dem Shopfloor zusammen und greifen bis zu der Auslieferung des Kundenauftrags ineinander.
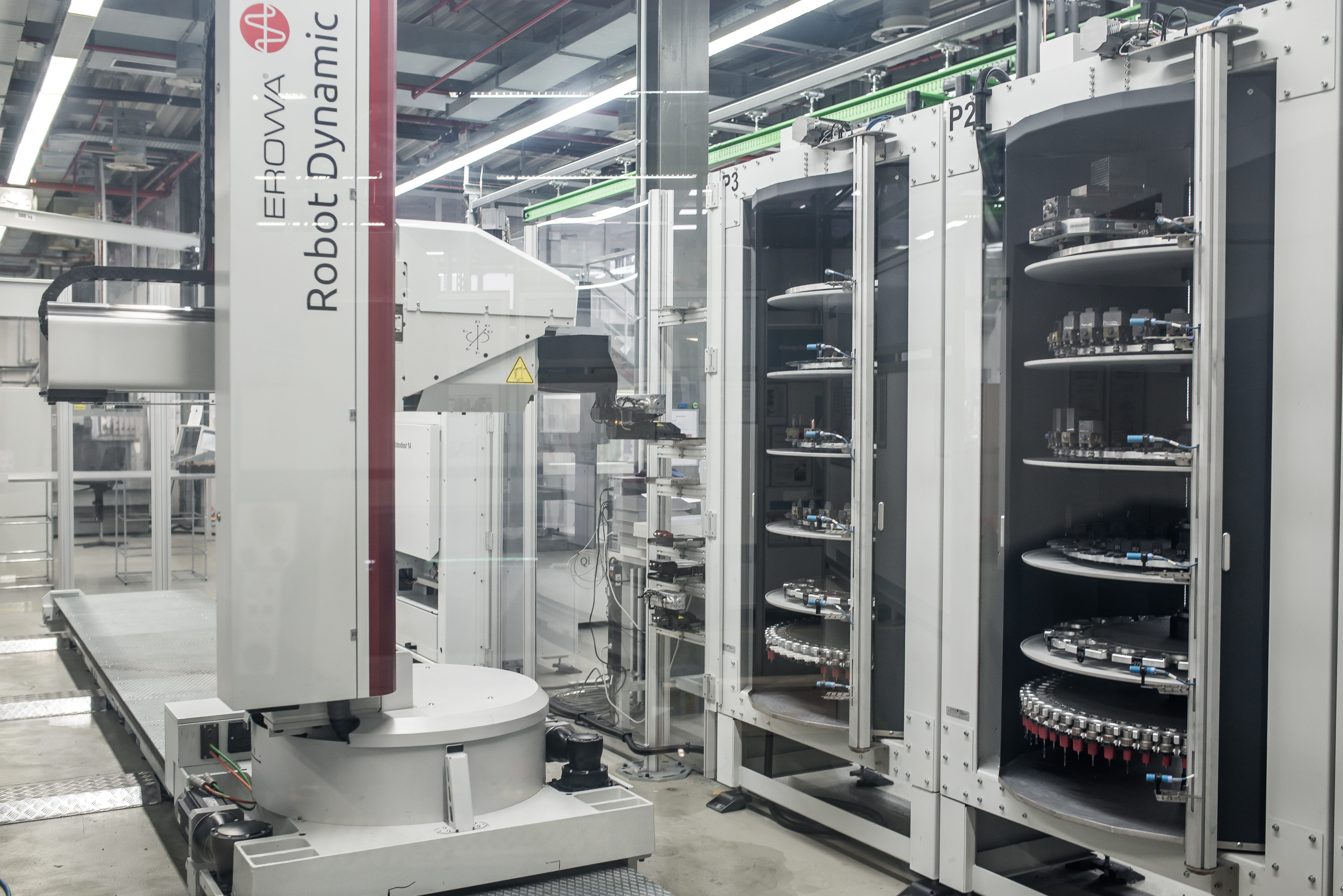
(Produktionszelle) Voll verkettete, automatisierte Produktionszelle im internen Werkzeugbau der Phoenix Contact GmbH & Co. KG als Beispiel für eine konsequente Umsetzung der Industrie 4.0.
Die digitale Plattform bietet dem Kunden eine vollumfängliche Flexibilität
Auf der digitalen Ebene werden bei Protiq manuelle Prozessschritte wie die Angebotserstellung, der Bestellprozess, die Produktionsplanung sowie das Materialhandling und die durchgängige Verfolgbarkeit von Aufträgen in einer automatisierten Prozesskette abgebildet. So kann in der additiven Fertigung besonders der große Vorteil der Schnelligkeit beibehalten und ausgenutzt werden. Der Kunde kann jederzeit flexibel seinen individuellen CAD-Datensatz auf der Webseite hochladen, analysieren und sogar automatisch reparieren lassen. Daraufhin erhält er neben einem visuellen Feedback seines Modells eine unmittelbare Auskunft über die grundlegende Herstellbarkeit, die Kosten für alle verfügbaren Materialien sowie die dazugehörige Lieferzeit. Nach Abschluss des Konfigurationsprozesses kann eine Bestellung über den Warenkorb sofort platziert oder als Projekt geteilt werden. Nach Auftragsvergabe durch den Kunden wird die Bestellung in das Warenwirtschaftssystem eingespielt, die Herstellbarkeit nochmals im Detail überprüft sowie in die Auftragsverwaltung und Produktionsplanung aufgenommen. Gleichzeitig wird der Liefertermin kommuniziert, wobei der Kunde auch fortlaufend über den aktuellen Produktionsstatus informiert wird. Über das Produktions-Planungs-System (PPS) wird der Kundenauftrag vom Zeitpunkt der Bestellung bis zu der Auslieferung digital begleitet und in jedem Prozessschritt mit weiteren Informationen angereichert. So entsteht parallel zum Produktionsprozess eine digitale Bauteilakte, die alle erforderlichen Informationen, wie beispielsweise Laufkarte, Messberichte, Baujoblayout und Design enthält. So kann eine identische Herstellung auch lange nach Abschluss des Auftrages sichergestellt werden. Besonders im Bereich der Serienfertigung ist dieser Faktor von großer Bedeutung, da die zuverlässige Reproduzierbarkeit sichergestellt sein muss.
Analoge Fertigung auf dem Shopfloor folgt dem Ziel einer intelligenten Vollverkettung
Parallel zum PPS verfolgt auch die analoge Fertigung bei Protiq das Ziel einer Vollautomatisierung und arbeitet derzeitig bereits in vielen Bereichen teilautomatisiert. So wurde im Jahr 2019 das gesamte Pulverhandling im Bereich des Kunststoff-Lasersinterns von der Pulveraufgabe, über den Pulvertransport bis hin zu der Pulverbereitstellung erfolgreich automatisiert. Hierbei wird das gesamte Pulverhandling über ein festes Rohrsystem realisiert. Die individuell entwickelte Steuerung synchronisiert dabei Neu-, Alt- und Baupulversilos, Auspackstationen sowie Sieb- und Mischeinheiten miteinander, wertet Bedarfe aus und sorgt für die automatische Bereitstellung von verarbeitungsfähigem Baupulver an den Lasersinter-Maschinen, sodass eine durchgehende Produktion und Fertigungslinie bei diesem Verfahren realisiert werden kann.
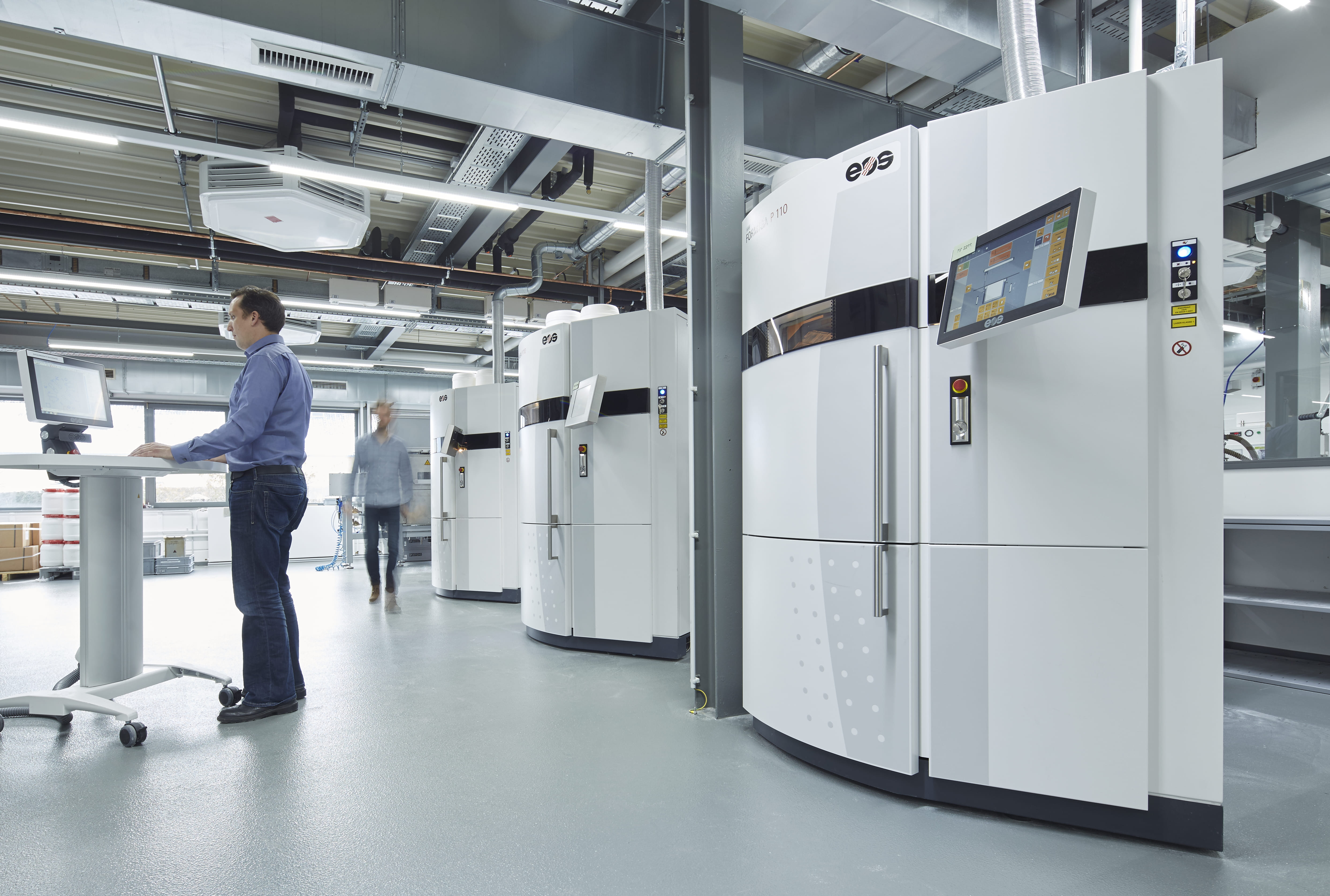
(SLS Bereich) Durch das automatisierte Pulverhandling werden die Anlagen im Bereich des Kunststoff-Lasersinterns kontinuierlich mit Baupulver versorgt.
Automatische Bauteilerkennung als Entscheidungsunterstützung in der Nacharbeit
Auch im Bereich der Nachbearbeitung und Qualitätssicherung greift Protiq bereits auf eine Teilautomatisierung durch die Nutzung eines entscheidungsunterstützenden Systems zurück. Diese eigens entwickelte Technik ermöglicht nach dem Bauprozess eine automatische Zuordnung aus einer Vielzahl von Bauteilen zu dem korrekten Auftrag. Besonders für das Kunststoff-Lasersintern ist dies von großem Vorteil, da in diesem Fertigungsverfahren die Möglichkeit besteht, in einem Bauraum nicht nur ein Bauteil, sondern eine beliebige Anzahl unterschiedlicher Bauteile herzustellen. Diese sind dreidimensional im Raum geschachtelt und müssen im Nachgang an den Herstellungsprozess wieder vereinzelt und sortiert werden. Die automatisierte Bauteilzuordnung basiert auf autonom arbeitenden Deep-Learning-Algorithmen - häufig auch als künstliche Intelligenz bezeichnet - und wurde speziell für diese Anwendung entwickelt. Durch dieses unterstützende System kann der Zeitaufwand bei der Sortierung drastisch reduziert werden, da der Bediener mehrere Bauteile auf einer Scanfläche ausbreiten, die Software starten und sich daraufhin einer anderen Aufgabe widmen kann. Sobald der Zuordnungsprozess abgeschlossen ist kann der gewünschte Auftrag ausgewählt werden. Die entsprechenden Bauteile werden daraufhin mithilfe eines Projektors farbig markiert und können zu sortiert werden. Neben der Reduzierung des manuellen Aufwands wird so ebenfalls das Fehlerpotenzial verringert.
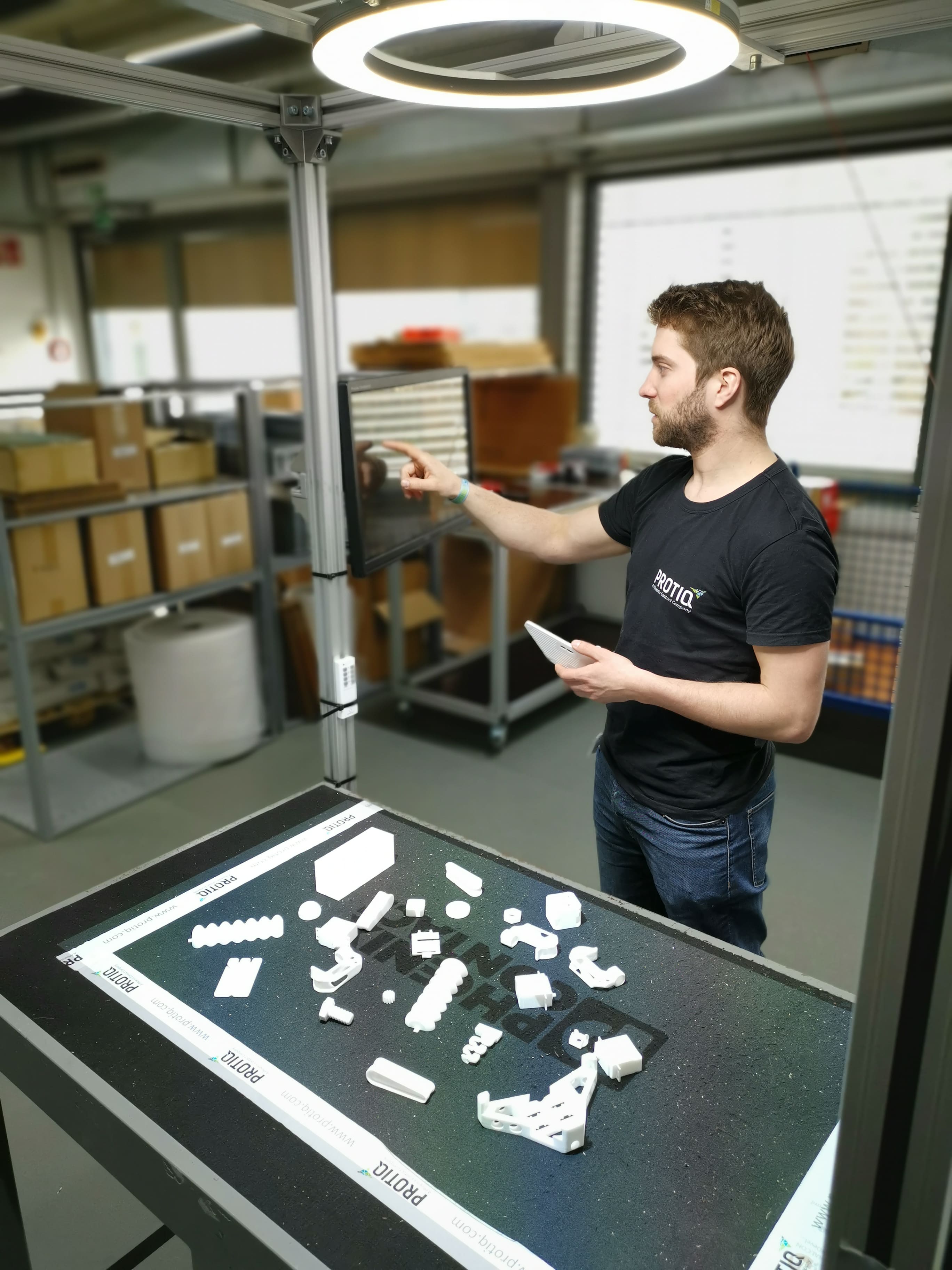
(Bauteilerkennung) Bei der automatisierten Bauteilerkennung wird industrielle Kameratechnik für die visuelle Erfassung unterschiedlichster Geometrien verwendet. Durch Interaktion mit einem Touchdisplay können über einen Beamer für jeden Auftrag die korrekten Bauteile farblich markiert und sortiert werden.
Die Transparenz für den Kunden als Begeisterungsmerkmal
Gemäß den Leitsätzen „Präzise. Schnell Zuverlässig.“ stehen für Protiq der Kunde und sein Bauteil im Vordergrund – im Zeitalter der Digitalisierung ist es von besonderer Bedeutung, eine höchstmögliche Transparenz zu bieten. Neben der Marktplatzfunktion auf der Protiq-Plattform soll der Kunde so nah wie möglich am Fertigungsprozess partizipieren. Die durchgängige Automatisierung bei Protiq auf der digitalen Ebene macht dies möglich und bringt insbesondere für die Serienproduktion Vorteile mit sich. Im Zielzustand soll der Kunde zu jedem Zeitpunkt genau wissen, in welchem Prozessschritt in der Produktionslinie sich seine Bauteile gerade befinden.
Weitere News
Ihre 3D-Dateien sind bereits fertig?
Laden Sie einfach Ihre Daten hoch. Alle Dateien werden automatisch geprüft und für den Druck optimiert.